Krwiobieg cywilizacji
Łańcuchy dostaw są krwiobiegiem naszej cywilizacji. Często nie zdajemy sobie sprawy jak skomplikowany proces prowadzi do tego, że możemy kupić marchewkę w warzywniaku, czy telefon w sklepie z elektroniką. Zanim produkt znajdzie się w sklepie musi zostać do niego przywieziony. Potrzebne są do tego samochody, statki, pociągi, palety, kontenery, wózki widłowe, paliwo i cała masa innych rzeczy (i pamiętajmy, że one same w sobie też są produktami). Żeby produkt mógł być przewieziony musi zostać wyprodukowany (lub wyhodowany). A do tego potrzebne są półprodukty, surowce, maszyny, energia (czyli kolejne produkty). Surowce trzeba wydobyć lub odzyskać (np. ze starych produktów), a energię wytworzyć. Do tego są potrzebne inne maszyny, transport, paliwo. Tworzy to wszystko bardzo skomplikowany system wzajemnych powiązań. Produkty, półprodukty do produktów, półprodukty do półproduktów, produkty do wytwarzania i transportu produktów i półproduktów… Wszystko to krąży po świecie i sprawia, że marchewka i telefony pojawiają się w sklepach, a my jesteśmy malutkimi trybikami tej maszynerii. Ale skomplikowane systemy bywają czułe na zaburzenia. Tak jak tzw. efekt motyla. W nauce nazywamy takie systemy chaotycznymi. Nie oznacza to wcale, że panuje w nich chaos, a właśnie, że małe zaburzenie może szybko doprowadzić do dużych zmian układu.
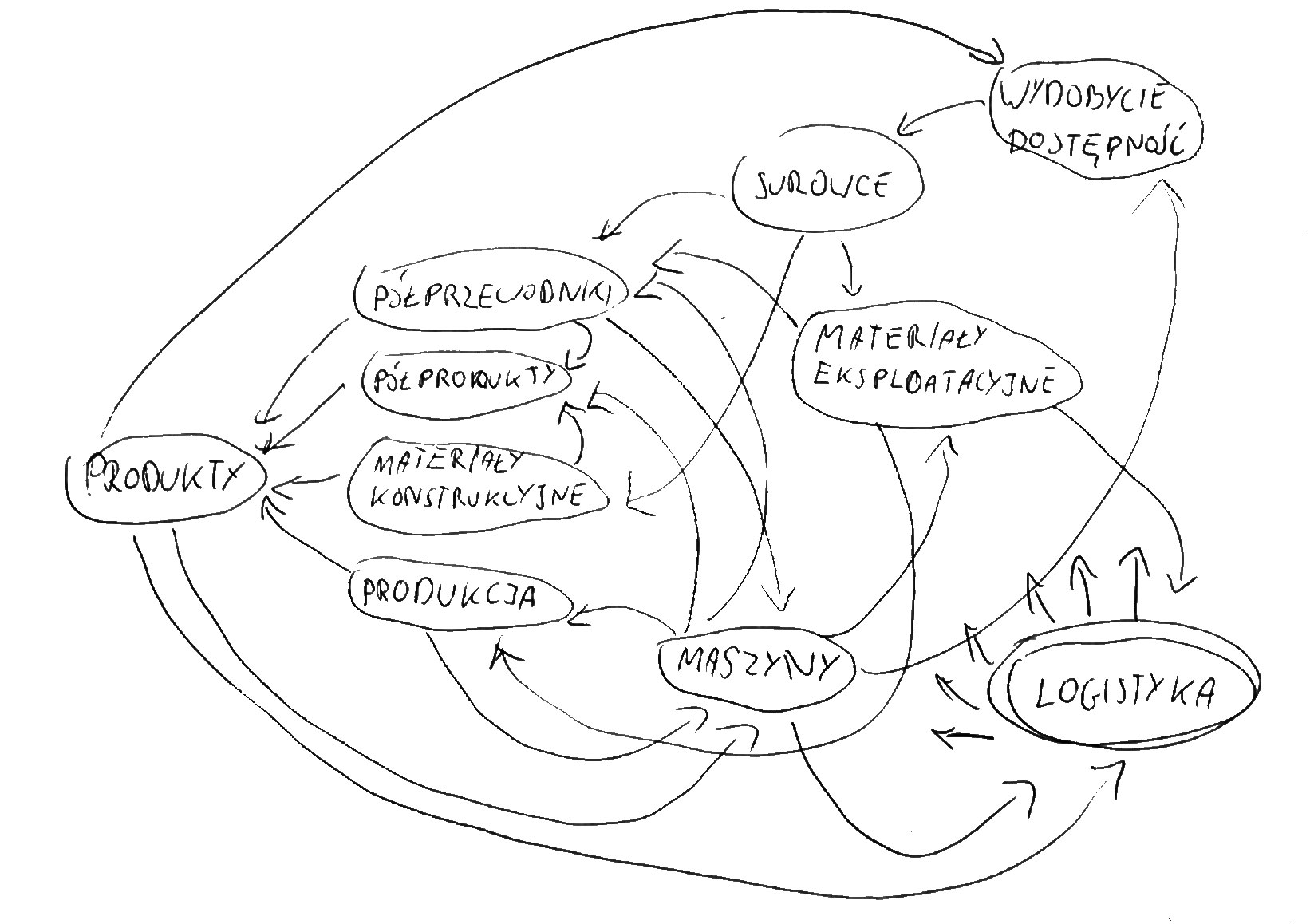
Zależności w łańcuchach dostaw potrafią być naprawdę poplątane
Te wszędobylskie chipy
Bardzo szczególnym rodzajem produktu (w zasadzie półproduktu) są półprzewodniki. Czyli wszystkie diody, tranzystory, procesory, chipy i inne komponenty, z których buduje się elektronikę. A to dlatego, że występują w bardzo wielu produktach, maszynach, samochodach itd. Są wszechobecne i zależy od nich działanie ogromnej części urządzeń. A dodatkowo ich produkcja wymaga bardzo skomplikowanego know-how, drogich maszyn (też wykorzystujących półprzewodniki) i rzadkich surowców. Tym bardziej to jest skomplikowane i drogie im bardziej zaawansowane chipy się produkuje. A to sprawia, że fabryk produkujących najnowocześniejsze procesory i pamięci jest dosłownie kilka na świecie. I nie myślcie sobie, że te najnowocześniejsze chipy to jakieś ultradrogie produkty o niszowych zastosowaniach. Nie, produkuje się je w milionach sztuk i są w naszych komputerach, telefonach, samochodach, serwerach dostarczających nam internet i te wszystkie chmury, sterują maszynami w fabrykach. Widzicie zatem jak czuły jest to punkt.
Wszystko zaczyna się rwać
O zerwanych i ponadrywanych łańcuchach dostaw słyszymy dużo i doświadczamy ich od czasu pierwszego lockdownu – a to nie było papieru, a to kamerek, drożały komputery, karty graficzne. A rozumiecie już chyba, że to tylko wierzchołek. Że nawet małe zakłócenie równowagi między popytem a podażą jednego produktu może wywołać całą falę zdarzeń. Ale lockdown (który z punktu widzenia mechanizmów łańcuchów dostaw był właśnie zaburzeniem podaży i popytu – nagle przestaliśmy kupować jedne produkty, a zaczęliśmy inne) nie był jedyną przyczyną i nawet nie pierwszą. Dużą, choć może nie aż tak gwałtowną zmianą było (i nadal jest) przechodzenie wielu usług i oprogramowania na model SaaS – słynna chmura. A to oznacza mniej komputerów i ich komponentów, a więcej serwerów, routerów i reszty sieciowej magii. A to oznacza mniej półprzewodników jednego rodzaju, a więcej innego. Zmiana planów produkcyjnych półprzewodników oznacza zmiany planów zamówień wszystkiego co jest potrzebne do ich produkcji. A jak widzieliście trochę tego jest. Dołożyło się do tego mnóstwo innych mniejszych lub większych zaburzeń: przeciągające się remonty terminali przeładunkowych, blokada Kanału Sueskiego przez kontenerowiec Ever Given, braki stali przełożyły się na braki kontenerów transportowych, pożar w fabryce AKM (jedna z tych kilku), strajk w STM (inny ważny półprzewodnikowiec), amerykańsko-chińska wojna handlowa, opóźnienie inwestycji w nowe fabryki. Swoje dołożyła wojna w Ukrainie, która wymusiła przesunięcie (wydłużenie) części ważnych szlaków handlowych (swoją drogą nieoczekiwanie skorzystała na tym Turcja), oraz wpłynęła na podaż ważnych surowców: krzemu, neonu, aluminium (niespodzianka – ważnych dla produkcji półprzewodników). Dodatkowo przemysł półprzewodników, jak wiele innych, już jakiś czas temu przerzucił się na model JIT – produkcja just in time. Zamiast trzymać duże stany magazynowe, produkują seriami pod przewidywane zamówienia. No i mamy lawinę. Producenci półprzewodników nie mają dostaw, generują opóźnienia, przeorganizowują produkcję, pojawiają się spekulanci wykupujący całe stany magazynowe poszukiwanych chipów, ceny rosną, zwalnia produkcja rzeczy zależnych od półprzewodników, w tym tych potrzebnych do ich produkcji, co powoduje dalsze opóźnienia…
Elektronika – jak to się robi(ło)
Co to wszystko ma wspólnego z EXATELem? Oczywiście jak każdy operator telekomunikacyjny kupujemy dużo routerów, switchy, laserowych nadajników do komunikacji światłowodowej i innego rodzaju osprzętu telekomunikacyjnego. Sprzęt drożeje, wydłużają się czasy dostaw, opóźnia się wchodzenie na rynek nowych urządzeń. Ale to wszystko daje się jeszcze jakoś zaplanować, poukładać i zarządzać ryzykiem. A ja chciałem opowiedzieć wam o czymś ciekawszym. Otóż w ramach różnych działań związanych z sieciami definiowanymi programowo (SDN) projektujemy własne urządzenia sieciowe (w czym pomaga nam nasz partner od elektroniki, firma FastLogic). Żeby nie musieć dopasowywać się do funkcjonalności dostępnych routerów i móc wykorzystać pełen potencjał drzemiący w SDN.
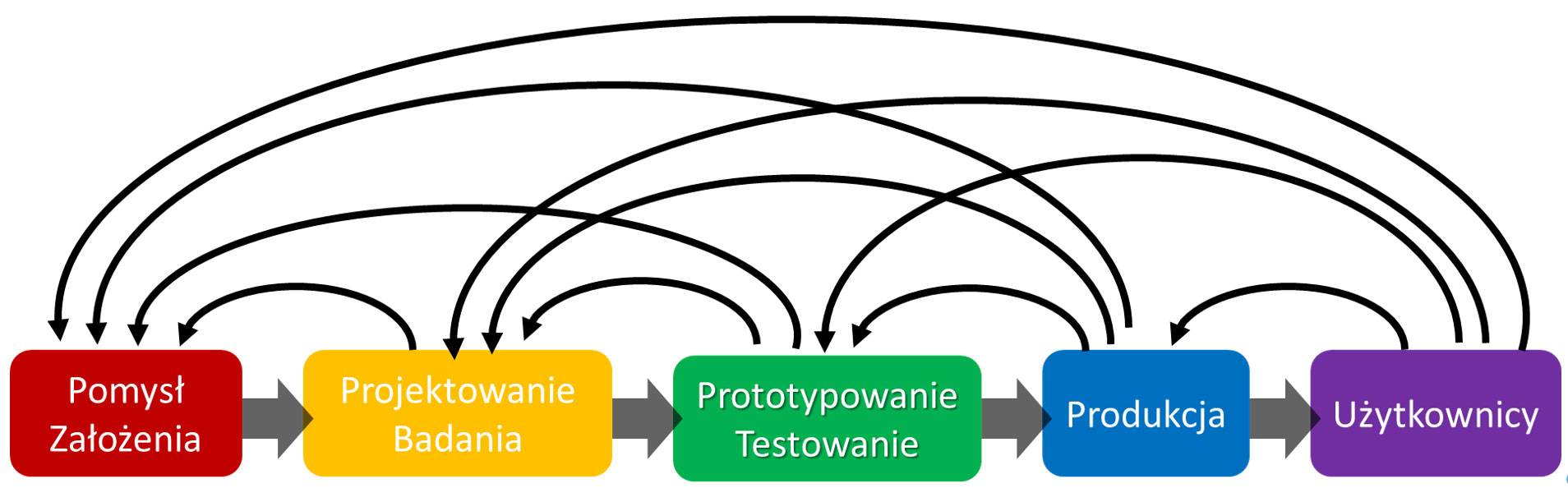
Cykl(on) projektowy – z każdego kolejnego etapu możemy być zawróceni do jednego z poprzednich, czasem nawet po kilka razy
Najpierw opowiem jak od lat wyglądał proces projektowania urządzenia elektronicznego.
Wpadamy na pomysł co chcemy zbudować. Wymyślamy funkcjonalności, opisujemy wymagania i specyfikację, określamy założenia kosztowe (ile max to ma kosztować) i czasowe (na kiedy chcemy to mieć). Potem dobieramy kluczowe komponenty urządzenia, które mają te wymagania spełnić: procesor, czy inne układy cyfrowe, główne komponenty zasilania, moduły komunikacyjne, czujniki itp. Wybieramy to z katalogów producentów kierując się dopasowaniem do funkcjonalności, łatwością implementacji (bo np. mamy już biblioteki dla danej rodziny procesorów), horyzontem wsparcia dla komponentów (żeby nie było, że za rok nam wycofają z produkcji główny procesor), no i oczywiście ceną – żeby nie wylecieć poza ramy budżetowe urządzenia. Przy czym nie wszystkie ceny i informacje techniczne da się znaleźć w sieci, czasem trzeba wejść w dialog z producentem lub dystrybutorem, co oczywiście wydłuża proces do tygodni. Robimy bardzo wstępny szkic płytki PCB, żeby sprawdzić jak duża ona wyjdzie i czy zmieścimy się w wymiarach dla urządzenia. Jeśli nie, to trzeba grzebać za mniejszymi, albo bardziej zintegrowanymi komponentami. A że wszyscy zawsze chcą jak najbardziej wypasionych, jak najmniejszych i jak najtańszych urządzeń, to takich iteracji przymiarkowych robi się zwykle co najmniej kilka zanim wszystko się zmieści w założonych wymiarach i pieniądzach (albo trzeba zweryfikować założenia).
Następnie zaczyna się faza badawcza. Zamawiamy te główne komponenty lub ich zestawy ewaluacyjne (zamawianie i czekanie na nie też trochę trwa) żeby je potestować i sprawdzić czy faktycznie spełniają nasze oczekiwania. Robimy różne eksperymenty „na brudno”, weryfikujemy założenia – czy to faktycznie da się tak zrobić, czy nie trafiamy na jakieś ograniczenia. Nie wszystko się udaje, wtedy musimy cofnąć się o krok. Kiedy wszystkie najważniejsze klocki są zebrane i wiemy, że działają razem i osobno, robimy projekt „na czysto” (jeżeli urządzenie jest proste) lub na „pół-czysto” jeżeli przewidujemy jakieś trudności (w takim wypadku dodajemy różne elementy, które nie są potrzebne w docelowym produkcie, ale ułatwią nam testowanie i rozwiązywanie problemów. Decydujemy też, czy robimy projekt od razu pod produkcję (co trwa dłużej), czy tylko pod testowy prototyp.
Potem zamawiamy płytki PCB, wszystkie komponenty, montujemy (co znowu trwa) i mamy prototyp, który możemy testować i tworzyć na niego oprogramowanie (część softu można było pisać już wcześniej, ale dopiero na prototypie można to zacząć robić na serio). Oczywiście wychodzą rozmaite problemy. A to jakieś błędy w projekcie płytki, a to te mniej ważne części nie działają do końca tak jak było w dokumentacji, a to okazuje się, że jednak nie zdołamy spełnić wszystkich pierwotnych założeń. Musimy się cofnąć o krok, a czasami nawet dwa lub trzy. I poprawki w projekcie, i kolejny prototyp i tak w kółko – aż zadziała. Za pierwszym razem nie ma szans żeby wszystko było super. Ale jak mamy szczęście, to za drugim będzie. Jak nie, to czasem i za dziesiątym. Za każdym razem prototyp jest trochę doskonalszy, robimy też ich więcej. Żeby więcej osób mogło to testować, żeby zbadać rozrzuty produkcyjne, no i na zniszczenie (jakie napięcie wytrzyma?).
W końcu któryś z kolei prototyp jest wystarczająco dobry żeby wyprodukować urządzenie w większej skali. Najpierw seria przedprodukcyjna, potem dopiero pełna produkcja. Bo tu też wychodzą problemy. Bo techniki produkcji w większej skali różnią się od prototypowych, bo dopiero większa skala ujawnia wady procesu montażu, bo okazuje się że końcowe koszty jednak są większe niż wynikało z wcześniejszych szacunków i na ostatnią chwilę trzeba coś potaniać, bo trzeba robić poprawki wynikające z badań certyfikacyjnych (a przeprowadzać je można często dopiero na egzemplarzach produkcyjnych).
No i nareszcie nasze urządzenie trafia w łapki końcowych użytkowników, którzy zaczynają z nim robić rzeczy, o których inżynierowie nie pomyśleliby w najczarniejszych snach. Ciekawe dlaczego zaczynają to robić dopiero na egzemplarzach produkcyjnych, a przy prototypach byli bardzo grzeczni…
Jak zatem widzicie kroków w procesie projektowania jest sporo, a w każdym z nich może nas spotkać konieczność cofnięcia się o jeden lub kilka. To trwa. No i procesy komunikacji z dostawcami, czekanie na części, czekanie na produkcję.
A co teraz?
Co się zmienia w tym procesie kiedy łańcuchy dostaw zaczynają krwawić? Na pomysły wpadamy jak dotąd, założenia i specyfikacje opracowujemy z grubsza tak samo. Ale kolorowo przestaje być już przy następnym etapie. Bo wybieramy sobie chip idealnie pasujący do naszych potrzeb. Pytamy dystrybutora za ile i na kiedy dostarczy nam kilka sztuk do testów. I dostajemy odpowiedź – cena przyprawia o zawał, a czas dostawy 53 tygodnie (autentyczna historia z naszego podwórka). Pytamy więc innych. To samo. Ale znajdujemy takiego, co ma 5 sztuk i chętnie nam dostarczy nawet za tydzień. Tylko cena jest razy 4. A będzie ich więcej potem? Nie wiadomo.
I tak jest z wieloma częściami. Czasy nie zawsze są aż tak długie, ale 3-4 miesiące trafia się już często. Na takie wydłużanie procesu projektowego (który i tak lubi się sam wydłużać) zwykle nie można sobie pozwolić. Więc jeśli do tej pory dobierając komponenty pytaliśmy się „co zapewni nam taką funkcjonalność”, „co będzie wystarczająco długo produkowane”, „co będzie wystarczająco tanie”, to teraz zadajemy tylko jedno pytanie: „co jest dostępne?”. Bardzo zawęża to wybór. Szukamy rzeczy, które da się kupić w kilka tygodni, i których dystrybutor ma wystarczająco dużo by starczyło na pierwszą produkcję. A funkcjonalność sprawdzamy tylko z grubsza. Bo lepiej mieć coś trochę innego, mniej dopasowanego lub nawet droższego niż nic nie mieć. Kupujemy kilka sztuk, testujemy i musimy szybko zdecydować czy dany komponent nam odpowiada. Bo musimy od razu kupić wszystkie egzemplarze potrzebne do produkcji. Przed prototypem, nawet przed projektem. Bo jeślibyśmy tego nie zrobili, to nie wiadomo czy ktoś by ich nam nie wykupił. A następna partia może za rok (bo producent ma kolejkę już i tak opóźnionych zobowiązań). I po cenie, którą podyktuje nam jedyny dystrybutor, który ma to w magazynie.
Więc nie dość, że są spore wydatki na początku procesu (kiedy wcześniej ich nie było), to jeszcze jest ryzyko, że pójdą na marne – bo kupujemy wszystkie egzemplarze, zanim zdążymy przetestować jak funkcjonują w kompletnym urządzeniu.
I to wcale nie dotyczy tylko „dużych”, kluczowych części jak procesory, czy pamięci. Z niewiadomych powodów z rynku potrafi zniknąć z dnia na dzień pewien rodzaj kondensatorów, czy przetwornic. Niektóre części są dostępne u wszystkich, po normalnych cenach. Ale jest ryzyko, że znikną. Na kilka tygodni, miesięcy, rok – nie wiadomo.
Sami widzicie – proces projektowy stanął na głowie. Nie da się do końca dobrać klocków do pomysłu, kupić klocki, zbudować, sprawdzić i kupić więcej takich samych klocków. Trzeba kupić klocki jakie akurat są i zastanawiać się co się właściwie da z nich zbudować. I pogodzić się z tym, że będzie to trwało dłużej, kosztowało więcej i że nie da się zrealizować wszystkich pomysłów. Ale jakoś sobie radzimy. Trzeba być jeszcze bardziej kreatywnym i elastycznym. Trzeba znajdować niekonwencjonalne rozwiązania. Trzeba budować urządzenia jeszcze bardziej modularne i tolerujące zmiany na ostatnią chwilę, by nawet już w procesie produkcyjnym dawało się zastąpić niektóre komponenty.
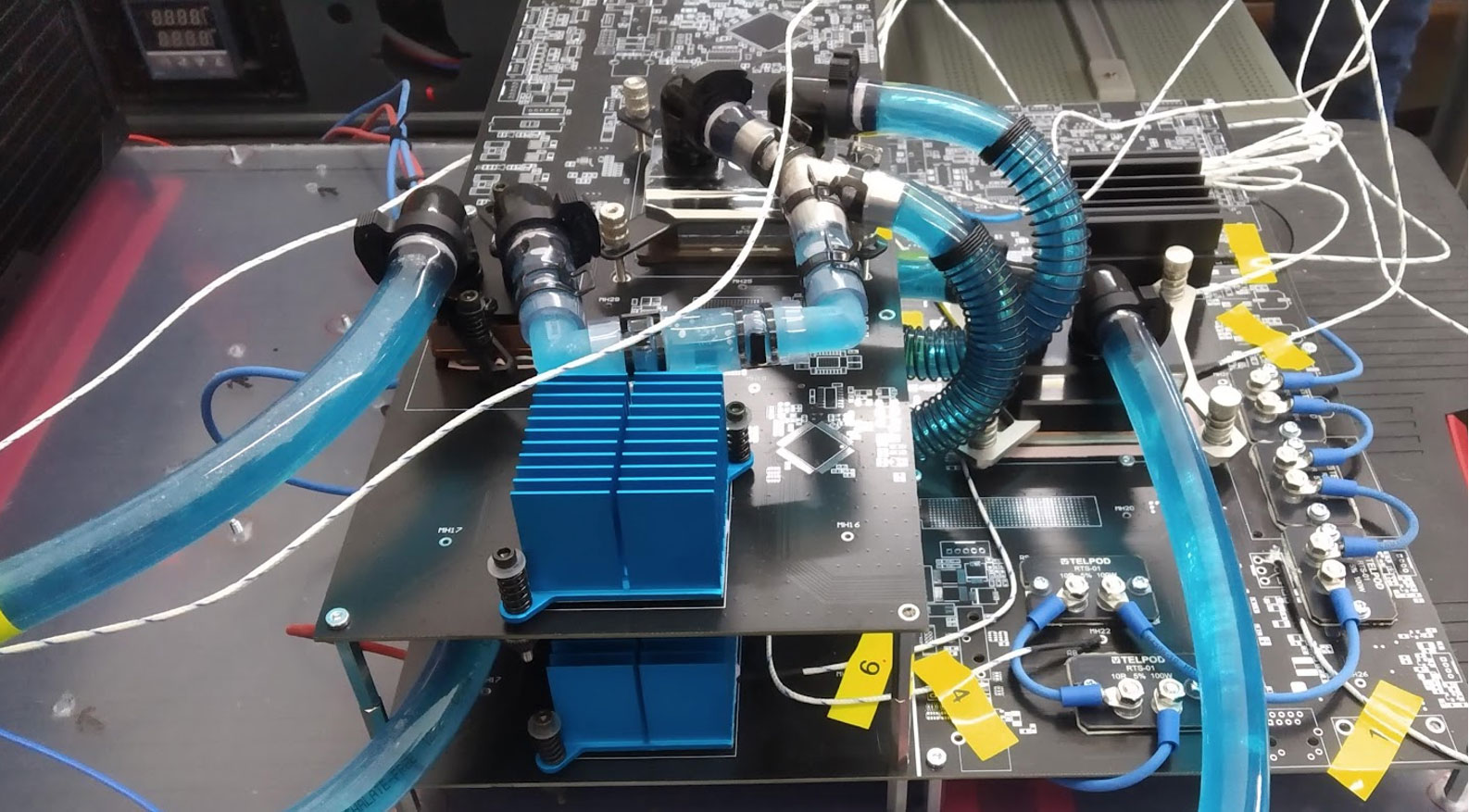
Jeden z prototypów urządzenia SDN EXATELa, na którym bardzo doświadczamy krwawiących łańcuchów dostaw. Ma swój własny błękitny krwiobieg chłodzenia.
I co będzie dalej?
Czy łańcuchy dostaw się odbudują? Czy krwawienie ustanie? Czy da się wrócić do starego, bardziej przewidywalnego i tańszego procesu projektowego? Gdy wydawało się, że sytuacja zaczyna się normalizować wybuchła wojna (a wraz z nią zaczęło brakować m.in. neonu potrzebnego w produkcji półprzewodników). Teraz wszyscy patrzą na Tajwan i Chiny, które roszczą sobie do niego prawa (a na Tajwanie zlokalizowane są bardzo ważne fabryki półprzewodników). Europa stara się zdywersyfikować źródła dostaw i choć częściowo uniezależnić się produkcyjnie, zwłaszcza w zakresie najbardziej zaawansowanych komponentów. Ale to olbrzymie i długie inwestycje. Myślę że jeszcze trochę tak pożyjemy. Łatwiej będą mieli ci, którzy projektują i produkują więcej różnych typów elektroniki, bo mogą mieć więcej stałych dostawców, dla których są ważnymi klientami, negocjować lepsze ceny, czy kompensować ryzyka pomiędzy różnymi projektami (kupiona niepotrzebnie partia przetwornic może się przydać gdzie indziej). Trudniej będą mieli ci, którzy mają mało linii produktowych lub – tak jak my – projektują coś od czasu do czasu. Ale dla naprawdę ambitnych i innowacyjnych projektów takich jak SDN, warto zacisnąć zęby i iść do przodu. Zawsze to trochę większa presja popytowa, a na koniec wynagrodzi nam to naprawdę unikalny produkt.